Statistics on Occupational Hazard
TTY has adopted preventive measures to address certain dangers in the work environment, including noise, heat, dust, specialized operations and organic solvents.
For employees who are exposed to special hazards such as organic solvents, specialized operations or noise, we provides them with protective gears (including face masks, gloves, goggles and lab suits) and strictly asks them to wear complete gears before commencing work activities. Furthermore, employees are instructed to handle organic solvents and hazardous chemicals only under the fume hood. To prevent noise hazard, ear plugs and ear muffs are provided to employees working in noisy environment, whereas specialized noise health checkups are arranged on a yearly basis. At factory sites, walk-around inspections and contractor safety management are conducted regularly to ensure that all personnel are able to complete their job duties with the utmost safety.
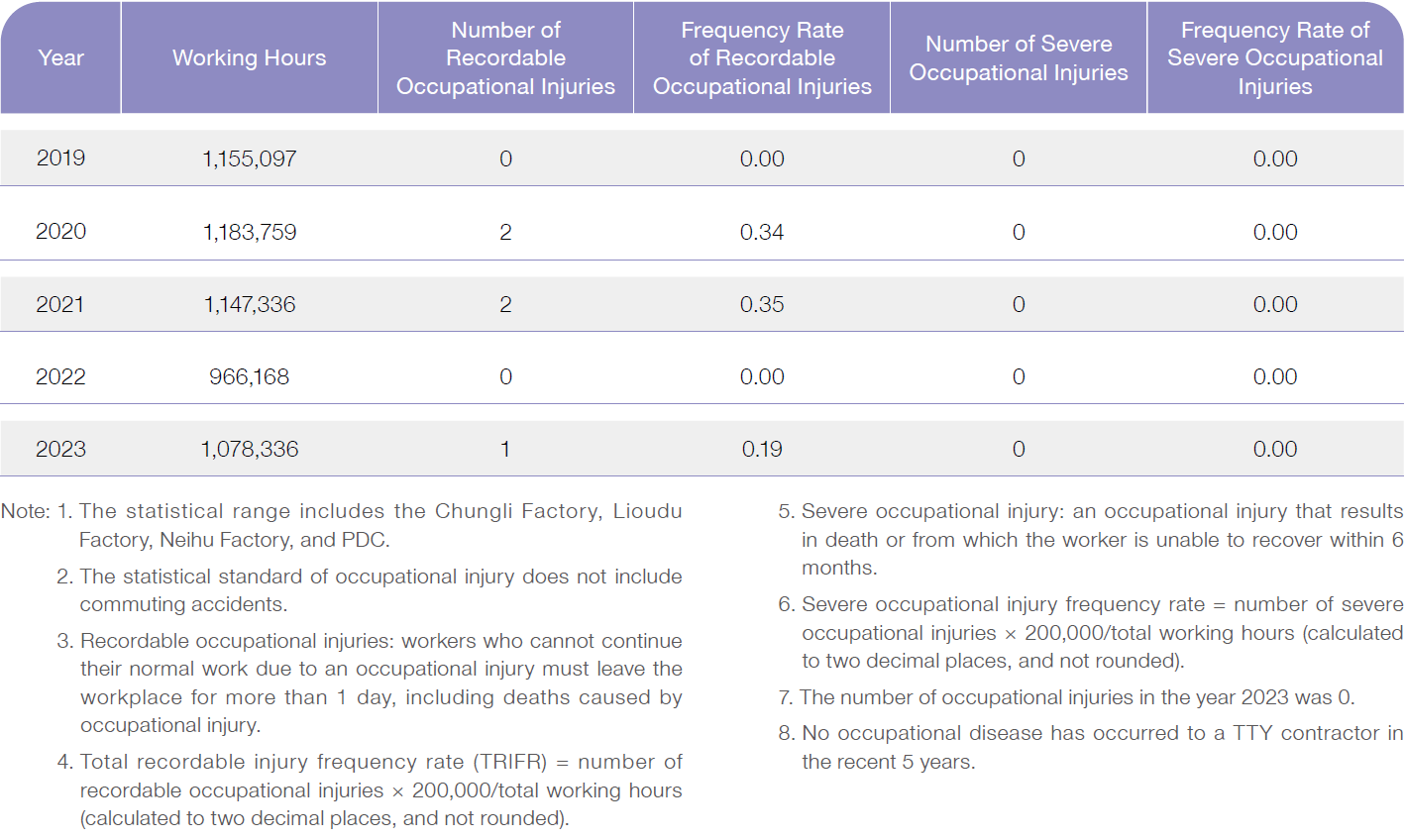
Protective Equipment
We value and protect the safety of each product we make. In the area of personnel safety, PPE (personal protective equipment) is used to keep our operators from certain occupational hazards. In accordance with relevant occupational safety and health laws and regulations, TTY carries out environmental harmful component inspections for different processes/production lines to assess the necessity and effectiveness of protective equipment and determine the working environment.
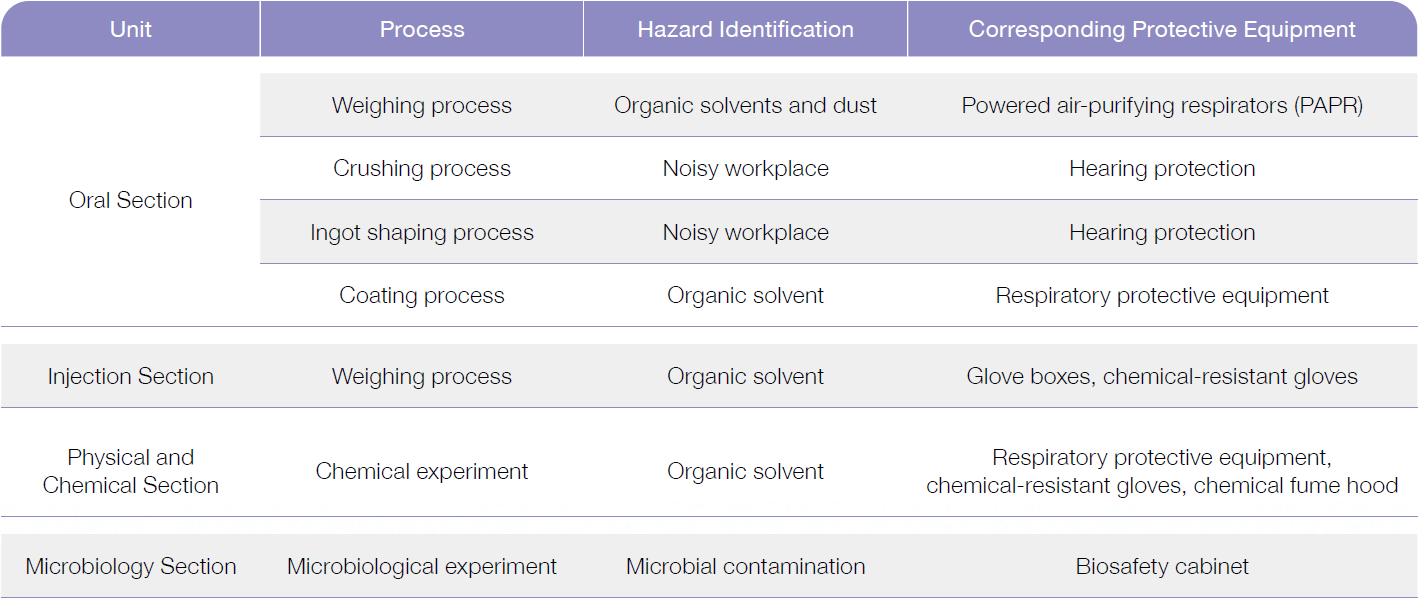
For example, glove boxes effectively allows factory workers to avoid contact with chemicals, and spill kits are provided for an immediate response to chemical spillages or leakages. This ensures that injuries can be contained and the disaster rate moderated. In addition, PPE is updated depending on the process requirements and use conditions so that production line employees receive maximum protection. For example, masks and protective clothing are all disposable and respiratory protective equipment is replaced according to the degree of dust adsorption.
Emergency Responses
TTY Biopharm uses a wide variety of chemicals. Relevant departments have formulated emergency response procedures to prevent dangers such as chemical leakages causing pollution of the environment, fires, and explosions. Chemical leakage handling, protective clothing practice, firefighting, evacuation, and emergency relief drills are conducted in cooperation with on-site departments on an annual basis to reinforce emergency response concepts and skills.
A chemical leakage treatment vehicle is dispatched to the factory, allowing employees to respond urgently and minimize the incident.
Employee Physical and Health Management
Health Management Degree |
1st Level |
2nd Level |
3rd Level |
4th Level |
Special Health Examination |
All findings normal, or part of the findings abnormal but overall deemed as normal by physicians. |
Part or all of the findings abnormal and overall deemed abnormal by physicians, but not work-related. |
Part or all of the findings abnormal and overall deemed abnormal by physicians but failed to establish the correlation between the results and the work. Further assessment by occupational physicians is required. |
Part or all of the findings abnormal and overall deemed abnormal by physicians, and are work-related. |
Pursuant to the regulations set forth in Article 6, Article 20, Article 21, and Article 22 of the Occupational Safety and Health Act, employers are required to conduct medical examinations and health checks. TTY Biopharm conducts health exams for employees of all factories. These exams include general and special health check items. The company offers regular and special exams for all employees on an annual basis.
In the year 2023, a total of 104 employees underwent special physical examinations, and their health management classification was implemented according to the regulations. If the health examination results are about personnel above level 2 management, nurses and professional medical specialists will perform health education and health follow-up examinations, and, if necessary, on-site assessments of suspected work-related injuries may be conducted. No personnel above level 3 management and no abnormalities in physical examinations caused by special operations were detected this year.
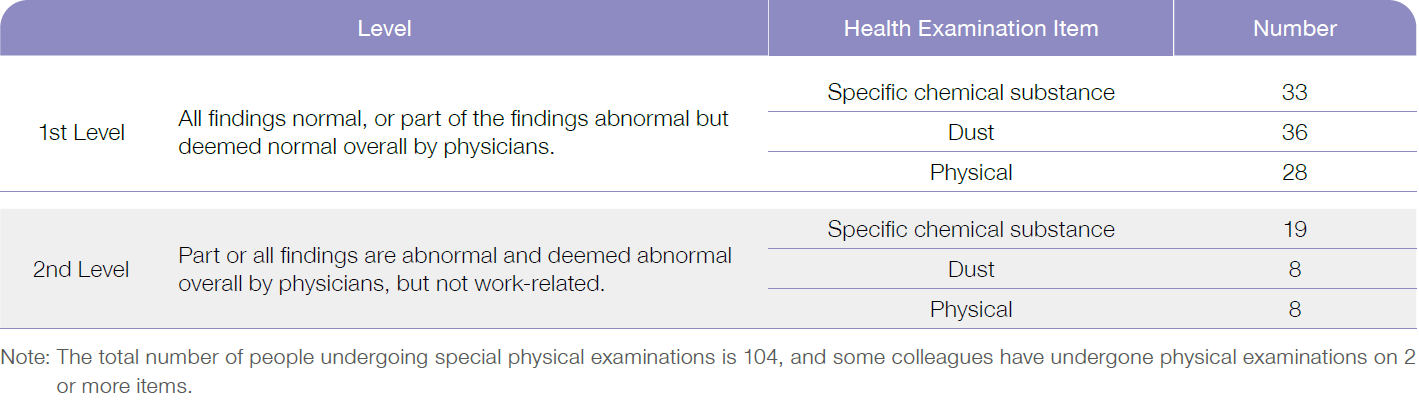
Safety and Health Workshops

After newly inducted employees report for duty, they have to participate in Work Safety and Health Workshops. This training makes employees familiar with them with the characteristics and dangers of various chemical substances (dangerous and hazardous objects) present in work environments or during operations inside factories as well as prescribed methods and operations.
When newly inducted employees report for duty in production areas, they are educated on the steps and procedures and important precautions pertaining to production process area operations by certified instructors before they are given access to production lines. Production unit executives constantly monitor compliance with operating standards and procedures by newly inducted employees. Non-complying employees receive guidance to ensure compliance.
Safety and health workshops (in accordance with production conditions) are organized on a non-scheduled basis to meet the needs of active duty staff. These courses are planned by labor safety and health administrators, while factory, production unit, and QC unit executives or other qualified personnel serve as instructors.
Personnel and Environment Inspections
During production processes, raw materials, personnel, and environments are key and indispensable components of product safety. All TTY factories therefore strictly abide by norms governing personnel and workplaces. Personal hygiene habits, hand hygiene, wearing and cleanliness of work clothes are required daily inspection items prior to initiation of production operations. Production environment inspections include machinery, equipment, packing materials, airborne microbes, and the quality of the water used for production processes in the factories to ensure implementation of various controls. These inspections guarantee that consumers are provided with safe, healthy, and worry-free products.